SAPHIR SYSTEM – one concept, maximum flexibility
The innovative SAPHIR SYSTEM from Weber Ultrasonics sets standards! Pre-configured for your specific needs, it is available as a manual workstation, a compilation of selected components or a custom solution perfectly adapted to your requirements.
Multifunctional – developing your process with the SAPHIR SYSTEM
The SAPHIR SYSTEM shows its true strengths when connected with other devices. It’s possible to realize machine concepts with up to 25 different functions. These functions range from the actual welding process and visual/mechanical inspections to sorting functions. Our engineers work with you to plan not only the technical concept but also the design of ideal weld seams and joints. Our proven development phase together with extensive testing in our Application Center assure you the optimum technical and economical solution.
Communication – the foundation for intelligence and safety
The communication capability built into the SAPHIR concept forms the basis for simple integration of the welding process in connected production environments. Standardized fieldbus systems such as PROFINET/PROFIBUS or Ethernet can be utilized. Optimum operational safety is ensured by functions that include complete documentation of all processing parameters, automatic backups and remote maintenance.
The SAPHIR Custom Solution
Tailored to your application
Our special strength in engineering is demonstrated by the design of innovative customized solutions. We work together with you to develop solutions tailored to your industry and requirements.
With our flexible modular system of high-quality ultrasonic components, we can implement exactly what you need for your most demanding applications.
You receive a turnkey system, complete according to the Machinery Directive, directly ready for use which features soundproofing enclosures, rotary indexing tables and additional functions, such as quality inspections or the option of performing several welding processes in succession.
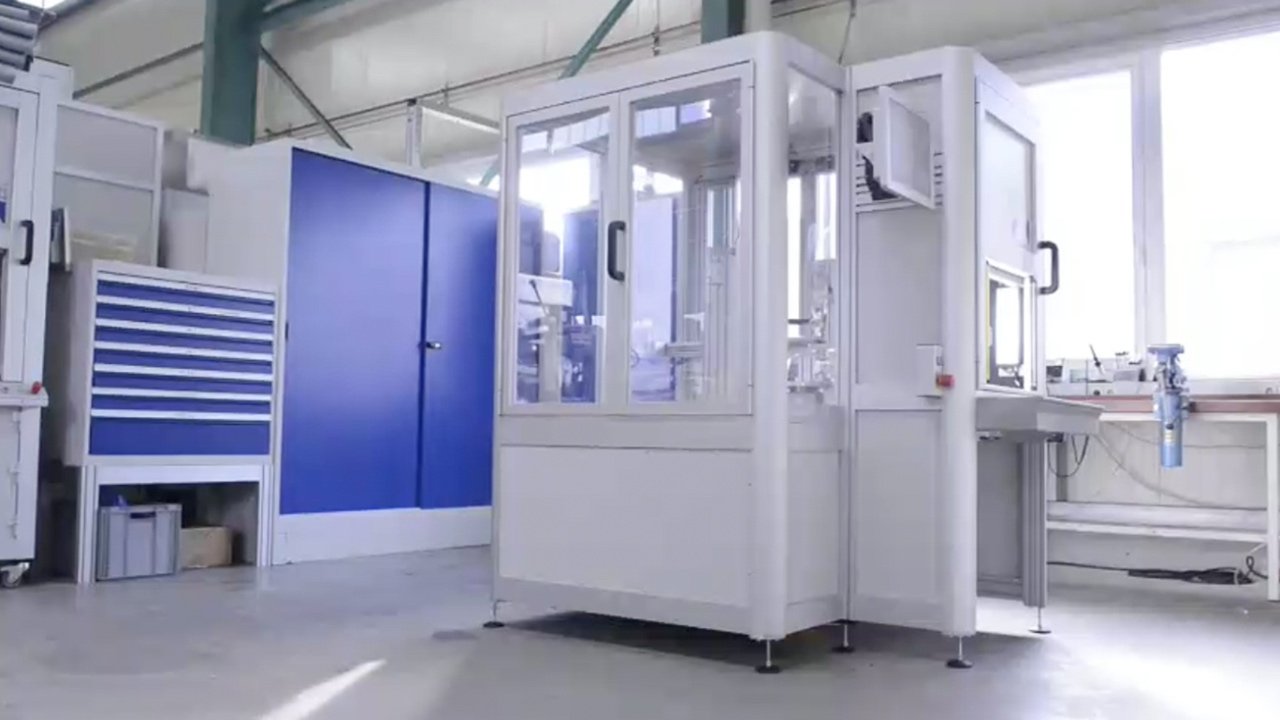
SAPHIR – integration-ready systems
The individual components of the SAPHIR SYSTEM
Take advantage of Weber Ultrasonics technology for your production process as demanded by your application. The innovative, highly modular SAPHIR system can be easily integrated in existing processes and adapted to your requirements. All components such as generator, feed unit, welding stack, Touch-PC unit with the powerful control software SAPHIR CONTROL 4.0, and other accessories can be pre-configured to suit your application.
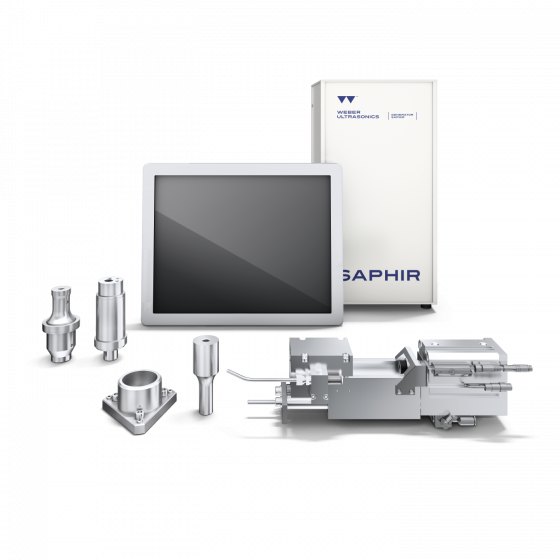
The SAPHIR SYSTEM as manual workstation
Innovative slicing and welding technologies in compact size
The space-saving plug-and-play all-rounder is pre-configured for you and ready for use.
It offers many different application and configuration options. The system can function as a partially automated or a stand-alone system , and comes equipped with quality components from Weber Ultrasonics.
- Simple operating concept
- 200 programmable welding processes
- Customization of welding processes
- Internet-capable for remote maintenance
- Interfaces: USB, PROFINET, PROFIBUS
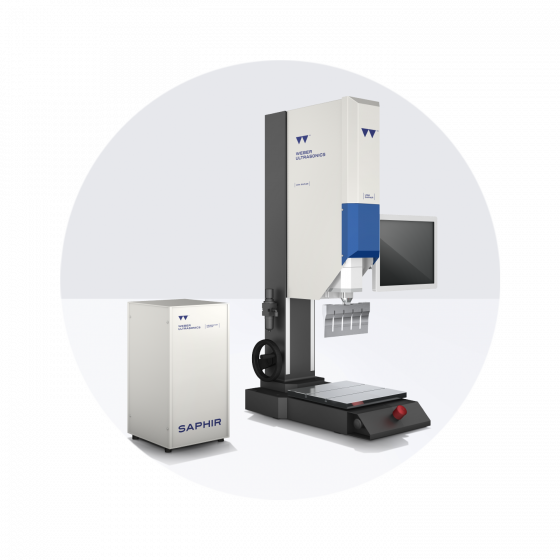
Die SAPHIR Module
The compact and robust construction of the feed unit allows simple integration in any automated system. It is available for ultrasonic welding stacks with frequencies of 20, 30 and 35 kHz, and also as compact unit.
The core of the Saphir system is the digital generator with power of up to 5,000 W. It is available with three standard frequencies of 20 kHz, 30 kHz and 35 kHz. The device, which operates reliably in ambient temperatures from -10 to +40 °C. Thanks to its compact design it can be easily integrated into existing systems. The Saphir Generator is also equipped with surge protection, temperature monitoring and many functions for process monitoring and control.
Welding stacks consist of converter, booster and sonotrode. They are always developed to fulfill customer or product-specific requirements with the help of Finite Element Method (FEM). High-quality materials such as titanium, CPM, aluminum and stainless steel are used in construction. The Quick-change module with indexed positioning increases flexibility and reduces set-up time.
The touch control module (available in 7-inch and 15-inch models) comes with extensive, intuitive-use software for Windows which gives you complete control over all major functions in the Saphir system at all times.
Visualization of the welding process simplifies the determination of optimum process parameters.
Features:
- – Documentation of all relevant processing parameters
- – Interface for data communication
- – Remote maintenance
- – Automatic back-up function
application engineering consulting
Customer inquiry
Weld design
Pilot Production
Testing in our
Application Center
System concept
Proposal and Purchase Order
Tool and system production
Process validation

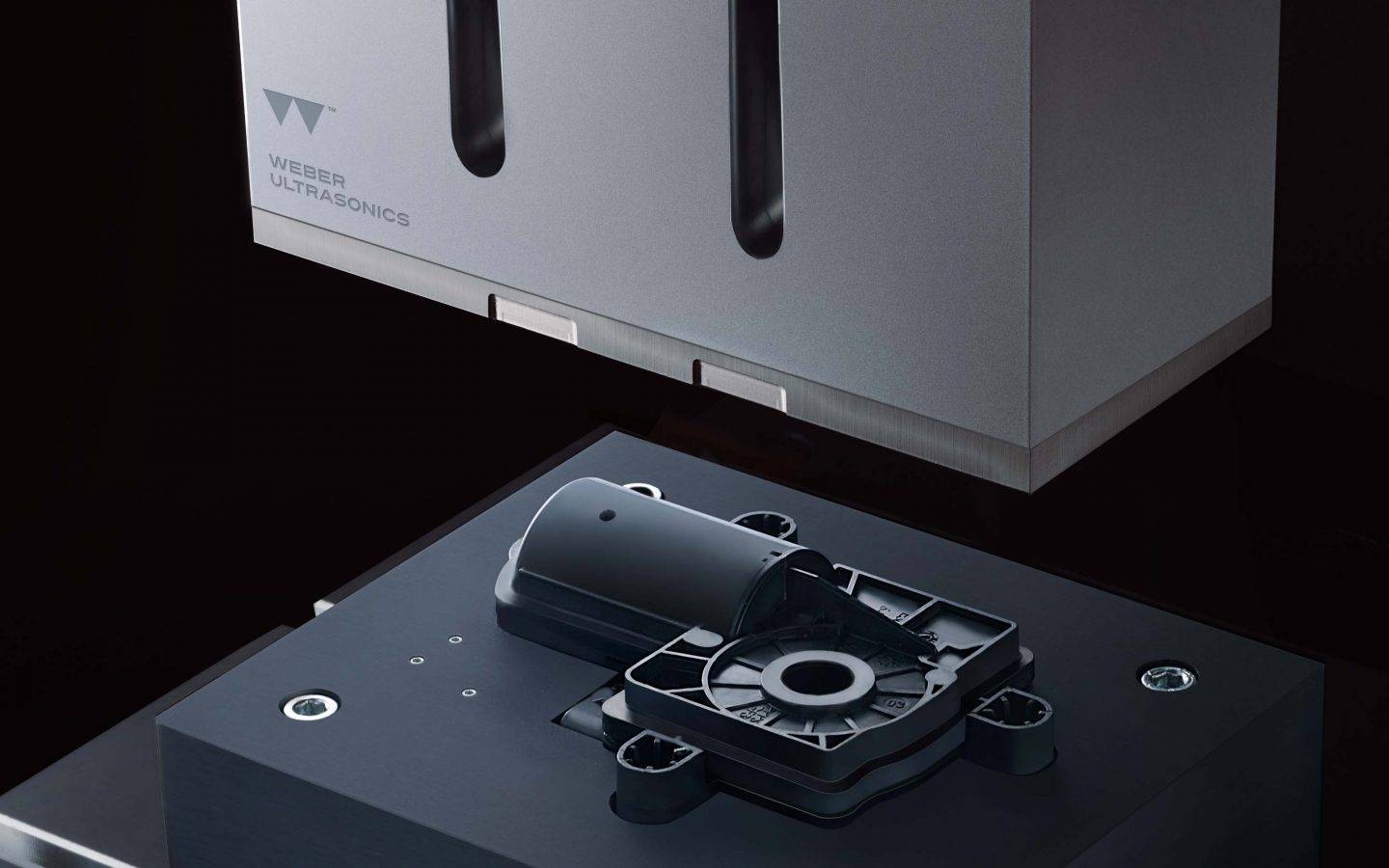
Events
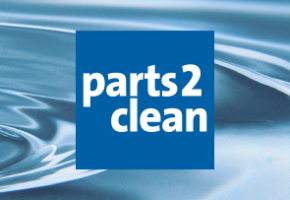
CLEAN SOLUTIONS FOR THE MANUFACTURING INDUSTRY
Optimum parts cleanliness: We'll show you how ultrasound technology optimizes industrial cleaning processes. Step by at our booth in Hall 10 B26!